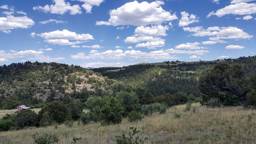
Photo: Peg McVay
In orienting this home’s layout on the site, Timbercraft capitalized on passive solar gain as much as they could while still building around the main priority: the view. As it stands, the kitchen will look toward Pike’s Peak, with many of the other windows facing “true south” to passively warm the home in the winter. One thing about timber homes, you usually don’t find them in a subdivision. They’re surrounded by a healthy acreage in the backcountry or perched on a cliff above a river or, in the case of the Peg McVay and Tony Stamm’s home, nestled along a hillside in the Colorado Rockies. The site of a timber home can be just as grand as its posts, beams and vaulted ceilings, and that means extra planning and preparation when it comes to site prep.
“In the three decades I’ve been building homes, we started with topography maps and I was walking every single site. Now, even in preliminary meetings, when we’re having our first conversation, we’ll bring them live on our screen and look at the satellite view,” explains Bob Sternquist, owner and CEO of Timbercraft, the timber framer behind the couple’s project. “Even just that view can show us if the property is appropriate for say, a walkout basement.” As it turned out, their site seemed suitable for a walkout, but there was too much bedrock to blast through, so what you can’t see is just as important as what you can. The team solved the issue by building the foundation to sit on top of the rock.
Site accessibility is important for every project, and if your land doesn’t have a driveway, that’s a good first step. Remember that log and timber packages aren’t going to come on pick-up trucks, they’re going to come on full-size semis. If your driveway is steep or has a switchback, then you’re going to need a separate staging area, where materials can be offloaded to a more manageable vehicle.
“My shipping company has always found that if their young drivers are able to get into our job sites, they’re a keeper,” says Bob. “For a project in Cincinnati, I was able to get a crane at the top of the hill, but I had to station a second crane at the bottom of the hill to hoist the package up to the crane at the top.” Fortunately, Bob says Peg and Tony’s materials were easier to manage: “We offloaded them at the bottom of the hill, then we had them ferried up to the job site with smaller trucks,” he explains.
As with everything else, the project was affected by the COVID-19 pandemic. Crews were universally delayed and building materials were in high demand and thus, more expensive. Peg and Tony had a solution to both these problems — they’ve been living on their property in an RV parked under a pole barn. Tony is a remodeler by trade, and living on the job site means it’s easy to lend a hand. This keeps the schedule moving along and adds sweat equity into their home. Since the couple is doing most of the interior finishes themselves, they’ll end up saving money on labor instead of eating the extra materials costs. Plus, knowing you are an integral part in building your home is a reward money simply cannot buy.
Take a look at: Dirt to Done Episode Two
Stay Tuned!
Join us as we navigate the design process with the homeowners and Timbercraft. You can find all the latest installments of the Dirt to Done series in the print magazine and here on timberhomeliving.com. Plus! Stay tuned for new webinars that dive into the process of creating this home.
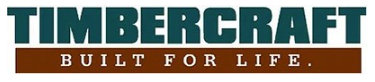